生成AI
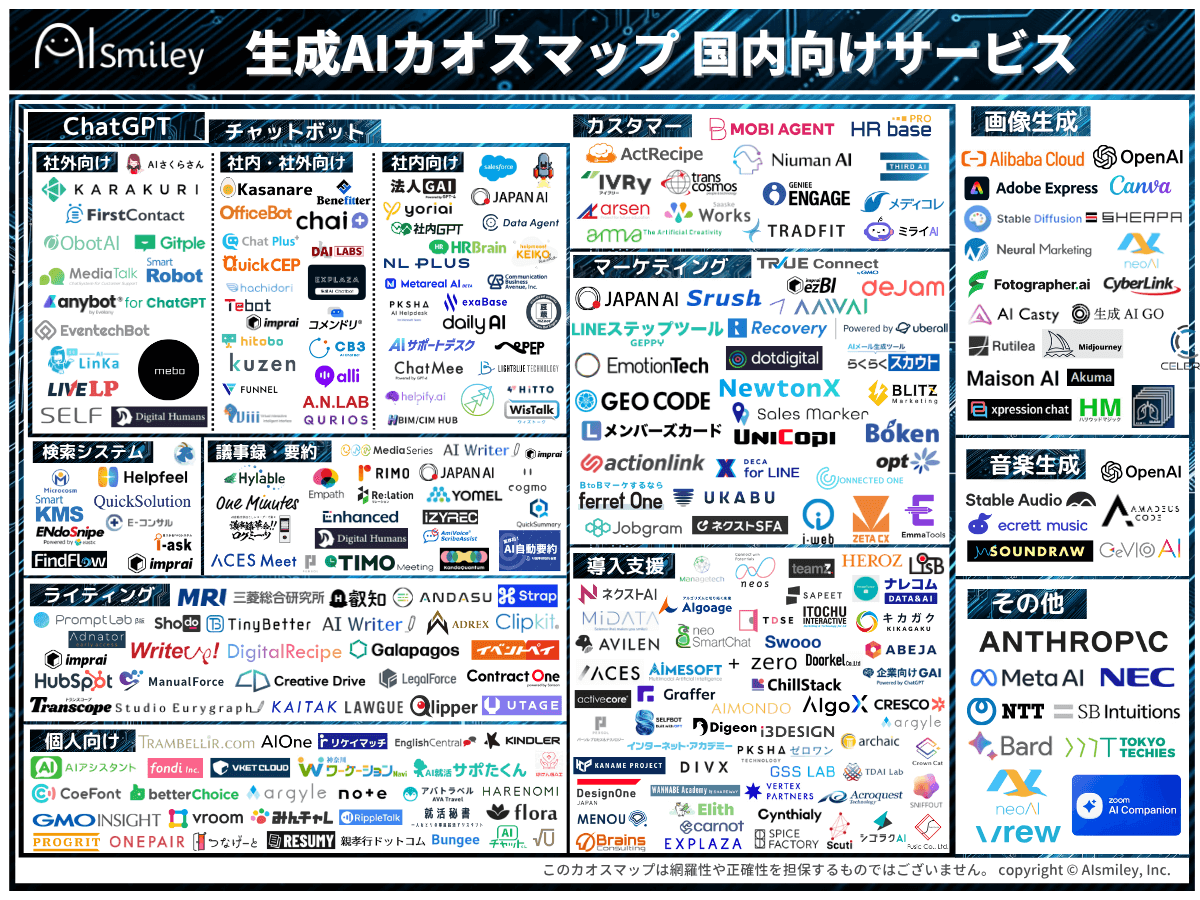
最終更新日:2024/02/27
Deep Consultingは、異常データが頻繁には発生しないような現場における異常検知を可能にするアルゴリズムの実用化に向けた研究を開始しました。
このAIニュースのポイント
Deep Consulting株式会社は、異常データが頻繁には発生しないような現場における異常検知を可能にするアルゴリズムの実用化に向けた研究を開始しました。研究およびクライアントへの提供を通じ、従来は熟練した作業者が時間をかけて検品する必要があった工程の自動化・効率化、達成を目指します。
製造業において、検品工程は自社製品の信頼に関わる重要な工程です。また、機械の構成部品に異常品が含まれていた場合、想定していない動作の原因となってしまうため安全面においても重要な役割を担います。
異常検知の手法として、最近ではディープラーニングによる手法が盛んに研究され、実用化においても主流とされてきました。
しかし、ディープラーニングを用いた手法には課題として主に以下の4点が挙げられます。
①正常 / 異常データの両方が一定以上ない場合、理想とする異常検出の精度が出ない
②データの収集に時間と工数がかかる
③一定以上、ディープラーニングの経験があるエンジニアが社内にいないと内製化できない
④外注するとしてもデータの収集は自社でする必要がある or 別料金のため高額になる
特に、異常が発生する頻度が極めて低い場合、正常データは集まっているが異常データが不足しているためにモデル構築ができないといった事例が頻発しました。
このような背景から、Deep Consultingは、少量の正常データのみからモデルを構築し、異常検知を可能とする手法を発明し、実用化に向けた研究を開始しました。
結果的に正常データのみ収集すれば異常検知が可能になりました。ディープラーニングを用いた通常の異常検知システム構築では、正常データと異常データが大量に必要でしたが、新たに開発したアルゴリズムによって、異常データを学習せず、かつ正常データも少量の学習で済むようになりました。それによりデータ収集を外注する費用の削減が見込めます。
また、システム構築期間の大幅、短縮化を達成しました。従来、満足のいく精度を達成するまで検証を繰り返し、その都度データの収集も追加でする必要がありました。そのため、システム構築には長期間かかることが一般的でした。
しかし、新たに開発したアルゴリズムでは、データ収集が少量の正常データのみで済むため、従来の手法と比べた際に格段にシステム構築期間を短縮することが可能になりました。また、費用削減に繋がりました。
Deep Consultingのアルゴリズムは以下のような場面において活用可能です。
自動車メーカーの生産ラインの電動機の故障検知
家電メーカーの生産ラインの設備の故障検知
電力会社の風車・太陽光パネルなどの発電機の故障検知
上記の例に限らず、時系列データを用いた異常検知であれば活用可能です。
Deep Consultingはアルゴリズムの研究および実用化を一層進めるとともに、時系列データの分析、動画データ自動モザイクAIなどとアルゴリズムを組み合わせることで、より広範囲なクライアントに向けてAIによる課題解決の支援を行っていく方針です。
業務の課題解決に繋がる最新DX・情報をお届けいたします。
メールマガジンの配信をご希望の方は、下記フォームよりご登録ください。登録無料です。
AI製品・ソリューションの掲載を
希望される企業様はこちら